● レポート
ハーモウェブセミナーレポート『eco(エコ)と段取り時間短縮に貢献する新製品のご紹介』2023/3/28開催
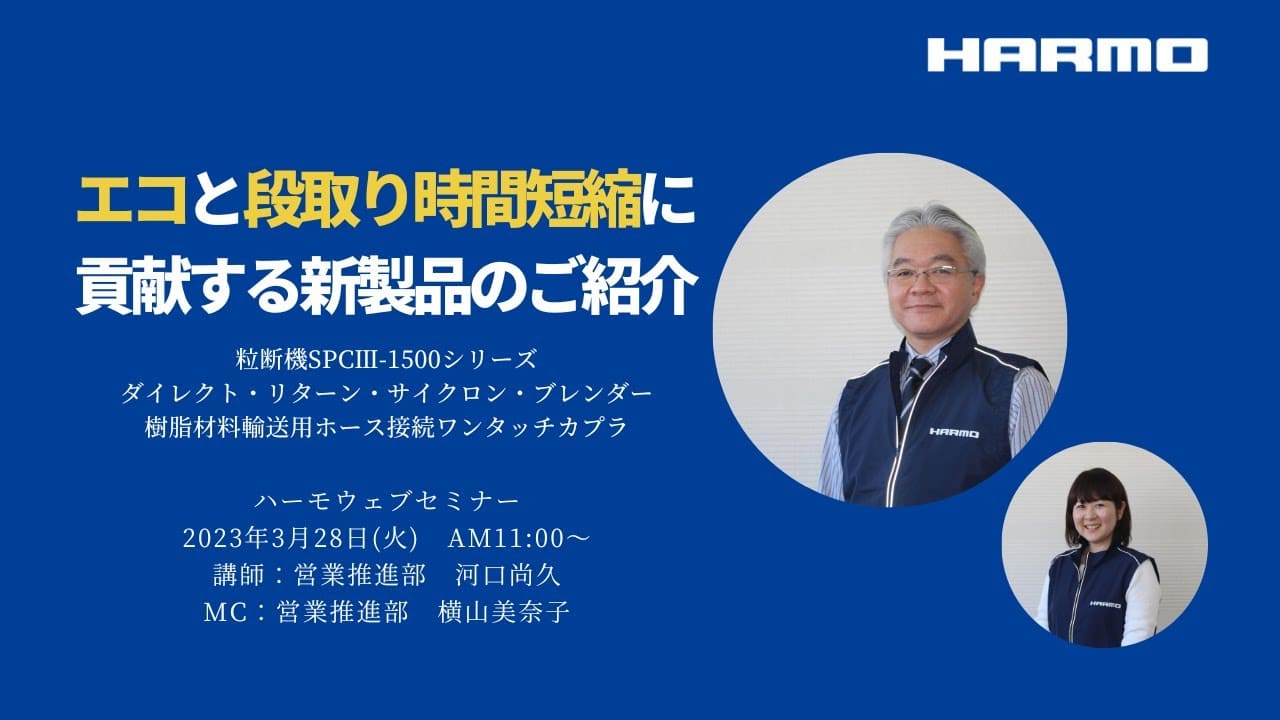
2022年3月28日(火)に開催したハーモウェブセミナー『eco(エコ)と段取り時間短縮に貢献する新製品のご紹介』の動画といただいたご質問への回答を掲載いたします。ぜひご覧ください。
ウェブセミナー資料をダウンロードできます
セミナーの資料をご用意いたしました。ダウンロードしてご活用ください。
ウェブセミナー内容
01. プラスチックのリサイクルの種類は?現状と企業の取り組み事例
3種類のプラスチックリサイクルとその利用先
マテリアルリサイクル
- 廃プラスチックを原材料にして再度プラスチック製品として利用すること
ケミカルリサイクル
- 廃プラスチックを化学的な処理をして分解し、原料にしてから再利用すること
サーマルリサイクル
- 廃プラスチックをガスや油などの固形燃料にしたり、廃プラスチックを焼却した熱を発電などに使用すること
プラスチックのリサイクルの手法と成果物
出典:一般社団法人 プラスチック循環利用協会『プラスチックとリサイクル 8つの「?」』
3つのリサイクルの割合
マテリアルリサイクル | 22% |
ケミカルリサイクル | 3% |
サーマルリサイクル | 60% |
未利用廃プラ | 15% |
出典:一般社団法人 プラスチック循環利用協会『26 プラスチックの3つのリサイクル』
企業の取り組み事例
株式会社BANDAI SPIRITS様
ランナーリサイクルの流れ
- 使用済みのランナーを回収
- 回収したランナーを粒断機で粉砕
- 粉砕したランナーを溶かして成形 → 新たなプラスチック製品へ
取り組み内容
- 使用済ランナーをその場で粉砕・成形し、新たなプラスチック製品にリサイクルする
- プラモデルのリサイクルの仕組みを知る機会を創出し、サステナブルの取り組みや、ものづくりの楽しさ、技術革新を解してもらうことが目的
- 使用済みのランナーを粉砕する機器として、ハーモの粒断機が採用されました
02. エコな新製品の紹介
マテリアルリサイクルのための新型粒断機
「SPCⅢ-1500シリーズ」
リサイクル材料による成形バラツキを低減する秘密
秘密はハーモ独自の「スイング・プレス・カット方式」
- ハーモの粒断機は通常の粉砕機と違い、樹脂を一定のサイズで連続切断が可能
- 粒もそろって、バージン材に近い形状のため、再生材による成形品質が安定
硬質材粒断例
一定の条件下でPEEKのリサイクルにも対応可能
- 金属代替樹脂と言われるPEEK(ポリエーテルエーテルケトン)は、スーパーエンプラとも言われ、その耐熱性・耐疲労性・耐磨耗性・寸法精度に優れることから、航空機の螺子やナットへの応用が期待されています。
- スーパーエンプラと言われる通り、品質性能に優れる反面、未だ樹脂価格は高額で、樹脂特性からリサイクルが難しい樹脂とされていました。
- 今般、PEEKのサンプルカットを実施したところ、一定の条件下にてリサイクルが可能であることが検証され、射出成形加工業者様への採用が決定しました。このように技術開発の進歩により、新たな樹脂が開発される昨今、今まではできなかった樹脂のリサイクルにもハーモの粒断機は貢献しています。
軟質材粒断例
リサイクルが難しい樹脂もハーモの粒断機でリサイクル率向上!
- PPやPE等のオレフィン系樹脂は、柔らかい特性を持っていることから、リサイクルしにくい樹脂と言われています。粉砕しても引きちぎったような切断となり、ブリッジを頻繁に起こし成形が止まってしまうため、リサイクルを諦めておられる射出成形加工業者様は意外と多い状況です。
- また、ウレタン系のエラストマー樹脂やゴム系の樹脂は、汎用の粉砕機ではそもそも切断できない樹脂が多く、射出成形加工業者様から、多くのご相談を頂いております。
- ハーモでは、プレス固定刃と移動刃のクリアランスを究極まで狭めることで、ウレタン系・ゴム系の軟質樹脂の切断が可能な軟質系樹脂専用の粒断機を開発。今まではできなかった軟質樹脂のリサイクルを実現いたしました。
バーションアップした粒断機「SPCⅢ-1500シリーズ」
粒断処理能力が1.33倍にアップ
モータ減速比を小さくして回転数を上げて揺動回数を増すことで、粒断処理能力が1.33倍になりました。
粗砕力が2倍にアップ
粒断処理能力1.33 倍と粗砕力アップ達成のため、粗砕力は減速ギヤの取付けで2倍になりました。
2. 材料のムダをなくす新製品!再生材を乾燥しない
「ダイレクト・リターン・サイクロン・ブレンダー」
※ダイレクト・リターン・サイクロン・ブレンダー=DBオプション
DBオプションのメリット
粒断材の再加熱による強度低下を抑えられる(品質安定)
「再乾燥」による課題
- PPSやアクリル系透明樹脂などは、過乾燥による製品の色調変化や流動性の変化による品質異常を引き起こすと言った課題もあります。
- DBオプションは従来の粒断材を乾燥機へ戻す方法よりも再加熱が1回減るので、成形品の強度低下を抑えることが可能です。
- また、再乾燥の必要ないリサイクル材を更に乾燥することによる無駄な電力消費の低減にも繋がります。
混合材を乾燥機に戻した時の余剰材が少ない(ムダを省く)
- バージン材と粒断材を一定混合して乾燥機内にストックした場合、成形終了時に多くの混合材が残ってしまう場合が多いです。そしてそれは多くの場合廃棄されてしまいます。そこで、乾燥されたバージン材と必要量の粒断材を成形機に必要分だけ送ることで、材料のムダを減らすことができます。
- また、成形後除湿乾燥機内に残る余剰材はバージン材のみなので、成形後の余剰材の管理も容易です。
ヘリカルホッパーにより材料の分離を防げる(安定成形)
ヘリカルホッパーによる樹脂の均一供給
- バージン材とリサイクル材が成形機ホッパーへ供給
- ヘリカルホッパーで攪拌混合されてから、射出バレル内へ均一に供給
- 成形品の品質異常を防止
乾燥機の清掃時間が短縮できる
- 粒断材をMDRⅡへ入れると、粉だけでなく小粒も乾燥ホッパーに静電気で付着するため、バージン材のみの場合に比べ、清掃時間が3倍多く必要となる。粒断材を乾燥ホッパーへ入れないことが清掃時間短縮になります。
(当社比10分→3分)
材料輸送のホースが1本になる
材料輸送のホースが1本になり、配管が少ないので成形機回りがスッキリします。
材料輸送中の吸湿を防ぐクローズ輸送が標準
成形機ヘリカルホッパーへ材料を輸送する際に二次エアを外気から取り入れません。ブロアからの除湿エアをバージン材タンクに入れて輸送します。
成形直後の粒断材の含水率測定
コラボ機は粒断材を成形機へ直接戻します。その時に問題となるのは、粒断材の吸湿です。粒断材の時間経過ごとの含水率を水分量測定器で測定しました。
測定日 | 2020年1月9日 |
湿度/温度 | 23℃/10% |
材料 | PA6 |
乾燥温度 | 120℃ |
金型温度 | 85℃ |
MDRⅠで乾燥バージン材水分量 | 218PPM |
粒断直後の粒断材水分量 | 339PPM |
粒断1時間後の粒断材水分量 | 632PPM |
粒断2時間後の粒断材水分量 | 891PPM |
結果
ポリアミドの成形可能含水率は1,000PPMです。いずれの含水率も成形可能な数値となっています。(余裕をみて粒断後1時間以内に成形機へ再投入します)
DBオプションについての動画
3. 簡単にできる材料ホースの脱着!
「樹脂材料輸送用ホース接続ワンタッチカプラ」
課題 多様化する樹脂の色彩への対応
色別に樹脂換えの頻度は上がり、段取り時間の短縮、生産性の向上に影響
- 多様化する成形品に対応して、さまざまな色彩の樹脂が供給されているため、樹脂の着色を専門に行なう加工業者へ依頼したり、マスターバッチを活用したり、ドライカラーを活用するなど、多様化する色彩への対応が行われています
樹脂換えの度に清掃するので、多くの作業時間が必要となる
- 射出成形の多品種少量生産においては、製品毎に複数の作業工程が存在。その中でも、樹脂換えに関しては「射出シリンダースクリュー内の樹脂換え清掃」「乾燥機の樹脂換え清掃」「樹脂を輸送するホースの樹脂換え清掃」があり、多くの作業時間を必要とします
樹脂輸送ホース脱着の課題
「安全性」と「段取り時間」への課題
- 成形機上のホッパーに締結されているホースの交換は、成形機上で工具を使っての作業となる
- そのため、ホースがはめ込まれている金属フランジとホースの密着度が高く、外しにくいため作業時間が掛かる
- 樹脂の種類や色が増えることでホース交換の作業回数は増加し、作業時間が増加する
材料ホースの脱着時間を劇的に短縮!
「樹脂輸送用ホース接続ワンタッチカプラ」
ワンタッチの着脱を動画でご覧ください
ホース1本当りの脱着時間はわずか数秒で完了
- 材料ホースをフランジに固定したままカプラを押し込んだ状態で、簡単にホースを脱着が可能。ホース1本当りの脱着時間はわずか数秒!
簡単操作で段取り時間を短縮。作業者の安全性も向上
- 工具を使いホースバンドを緩め、ホースとフランジの両側を把持したままホースをひねって外す作業と比較すると、格段に段取り時間を短縮
- また、工具を使わずホースの脱着を行えるため、成形機上の高所作業による工具の落下事故防止や、作業者自身の安全確保も実現
成形現場の省エネや時間短縮についてご相談ください
省エネは時間短縮はハーモの周辺機器導入で解決できるかもしれません。お気軽にご相談ください。
ウェブセミナー資料をダウンロードできます
セミナーの資料をご用意いたしました。成形現場の課題解決にダウンロードしてご活用ください。
ウェブセミナーの動画をご覧いただけます