スイングロボット選択の基準
スイングロボットにはどのような価値があるのか
外観上の品質を求められない機能部品は、成形後自動落下で箱に貯め置きされ、スプルランナーをスイングロボットで取り出す生産方式が一般的です。
横走行型ロボット比較するとスイングロボットは価格も安価で機能も単純であることから、多くのお客様は「今までと同じ機械を選択する」「成形機販売商社や成形機メーカーが勧める機械を選択する」「作業者が慣れているから選択する」などの基準で導入を決定されているのではないでしょうか。
このため、スイングロボットにはどのような価値があるかを選択基準とされるお客様が意外と少ないかもしれません。
スイングロボットで意外と気付いていない価値基準
取出し時間
ハイサイクル成形による製品取出しにおいて0.1秒を争う成形を行っているお客様がいる一方で、スイングロボットのランナー取出し時間を意識されているお客様は意外と少ないのではないでしょうか。
「成形サイクルに間に合っている」「なんとなく見た目が早く動いている」「他に優位性を持った代替品を知らない」などを理由に、取出し時間短縮による価値基準に気付かずスイングロボットを導入されているお客様は多いのではないでしょうか。
段取り時間
エアー駆動のスイングロボットは駆動源である圧縮空気を減圧してから、メカニカルストッパーを動かし、取出し位置を調整する必要があります。 この作業は成形機上へ作業者が登り、位置を目測しながら粗調整を行った後、最終微調整を行う必要があり、場合によっては二人の作業を必要とします。
このようなスイングロボットの段取り替え作業に対して疑問を持たずに作業が行われているのが実態で、段取り時間短縮による価値を意識されているお客様は、意外と少ないのではないでしょうか。
作業安全の確保
エアー駆動のスイングロボットは、成型機上で工具を使った作業を伴います。
「工具が滑って成型機上から落下し金型を破損させてしまった」「落下した工具が粉砕機に入って多額の粉砕機修理費用が発生した」「成形機への昇降の際に足を踏み外しけがをしたことがある」などのお客様の声をお聞きします。
スイングロボットを選択する際に作業安全の確保は見逃せない重要な価値基準であると言えそうです。
ゲートカット機等の二次加工機と正確な成形品の受け渡し
自動車の機能部品を生産されているお客様では、成形性の良いサイドゲートの成形品を成形されています。
サイドゲートはゲートカットを必要とし、スイングタイプロボットと自動ゲートカット機を組み合わせて全自動成形を行うケースがあります。
エアー駆動のスイングタイプロボットでは、型外へロボットアームが伸びた際、停止状態でロボットアーム先端が揺れるます。そのため、正確にゲートカット機へ成形品を受け渡すことができず、ゲートカットミスによる不良が出てしまう課題があります。
ロボットストロークの任意設定
エアー駆動のスイングタイプロボットは、金型内のロボットアームのストロークとスイング後の金型外のロボットアームのストロークを変えることができません。
必要以上に型外でロボットアームが伸びるため、無駄に成形機間隔を取ってしまいます。
逆に、金型内のロボットストロークが短いために金型外のロボットストロークが十分取れず、スプルランナー解放時に粉砕機までロボットアーム先端が届かず、粉砕機の位置調整を金型毎に行う必要があるといったの課題をお聞きします。
2軸サーボスイングロボットの価値分析と効果
2軸サーボ駆動のスイングロボットは取り出し時間が0.8秒~1秒早い
比較したロボット
- 2軸サーボ駆動のスイングロボット
- エアー駆動のスイングロボット
実成形でスプルランナーの取出し時間を計測してみたところ、エアー駆動のスイングロボットと比較して、2軸サーボ駆動のスイングロボットの取出し時間は、0.8秒~1秒早いことが分かりました。
取出し時間の短縮
生み出される価値分析(例)
- 成形サイクル 30秒
- 一日の稼働時間 16時間
- 月稼働日数 21日
- 1時間当たりの成形機チャージ ¥3,000
取出し時間が0.8秒早いと
上記の場合、 取出し時間が0.8秒早いと成形サイクルは29.2秒に短縮され、年間の効果は¥331,397となります。
取出し時間が1秒早くなると
成形サイクルは29秒に短縮され、年間の効果は ¥417,103となります。
段取り時間の短縮
生み出される価値分析(例)
エアー駆動スイングロボットの段取り作業プロセス
- 工具の準備
- 成形機上へ上りスイングロボットの圧縮空気を減圧する
- 工具を使い上下・前後のストッパを緩め位置調整を行う
- 成形機から降り、金型内の位置を確認し微調整を行う
- 再度成形機上へ登りネジを増し締めし、圧縮空気を昇圧する
- 成形機から降りて自動運転の動作を確認する
- 所定位置へ工具を戻す
サーボ駆動スイングロボットの段取り作業プロセス
- ロボットコントローラの動作メモリを呼び出す
- ステップ動作で上下・前後ストロークを確認
- 自動運転の動作を確認する
成形機を早く稼働させる
生み出される価値分析(例)
- 段取り時間短縮 12分
- 月の段取り替え回数 10回
- 1時間当たりの成形機チャージ ¥3,000
- 12分 × 10回 × ¥3,000 ÷ 60分 × 12か月=年間の効果は¥72,000/年
作業者が別の作業をする
生み出される価値分析(例)
- 段取り時間短縮 12分
- 月の段取り替え回数 10回
- 1時間当たりの人件費¥1,600
- 12分 × 10回 × ¥1,600 ÷ 60分 × 12か月=年間の効果は¥38,400/年
作業安全の確保
生み出される価値分析(例)
金型破損のケース
- 金型修理費 ¥500,000(金型修繕期間、2週間の生産停止)
粉砕機破損のケース(例)
作業者負傷のケース(例)
- 労災認定による企業イメージの低下、労災保険料の全額会社負担と休業補償
- 休業中の代替人員確保、時給¥1200円のパート社員の採用2か月
- ¥1,200 × 8時間 × 21日 × 2か月= ¥403,200(疾病休業期間の損失)
正確な成形品の受け渡し
生み出される価値分析(例)
ゲートカット不良を解決する2軸サーボ駆動スイングロボット
2軸サーボ駆動スイングロボットは型外でのロボットアームの正確な停止位置と、任意の速度選択により、ロボットアームの先端が揺れることが無く、正確にゲートカット機へ成形品を受け渡すことができます。ゲートカット不良による製品歩留まり低下の課題を解決します。
エアー駆動スイングロボットとゲートカット機の受け渡しミスによるゲートカット不良の損失
2軸スイングロボット導入による効果は年間¥540,000
- 月間の成形品の生産高 100万円
- 受け渡しのミスによるゲートカット不良率 3%
- 100万円 × 3% × 12か月 = ¥360,000(年間不良品発生による損失)
- ¥360,000 × 製造原価率 50% = ¥180,000(不良品を作り直す際の損失)
ロボットストロークの任意設定
生み出される価値分析(例)
2軸スイングタイプロボットは金型内のロボットアームのストロークと金型外でのロボットアームストロークを任意に設定することができます。このため、必要以上に隣の成形機との間隔を確保する必要がありません。
また、粉砕機までロボットアームが届かず、粉砕機の位置調整を金型毎行ったり、特別なシューターを設置する等の課題も解決できます。
金型毎の作業負荷
生み出される価値分析(例)
2軸サーボスイングロボット導入による効果は年間 ¥24,000
- 段取り替え 月5回
- 金型毎粉砕機とロボットの位置の再調整一回当たり 15分
- 作業者時間当たりの労務費 ¥1,600
- 5回 × 15分 × ¥1,600 × 12か月=¥24,000(年間無駄な作業負荷による損失)
生産性向上でお悩みの企業様はご相談ください
- スイングロボットを使っているが今より生産性を向上させたい
- 製造原価を低減させたい
- 段取り時間を短縮したい
- 作業安全を確保したい
- 品質を向上させたい
これらの課題を解決されたい成形加工業者様はぜひハーモにご相談ください。

ハーモの2軸サーボスイングタイプ取出ロボット
EXZⅡ-600(F)/800(F)
Z軸とY軸にサーボモータを採用
- 取出しタイムを35%短縮(参考 旧EXZ-600:対比35%、EXⅢ:対比45%)
- 内部金型メモリからティーチングデータの読み込みが可能。金型交換時のストローク調整が不要となり作業効率が向上します。 (ティーチング後、50型)
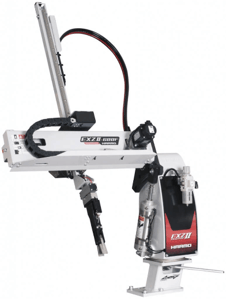
EXZ-II の製品ページを見る
関連記事