成形工場の省人化は様々な課題解決に
射出成形工場の省人化は生産性向上、人手不足解消、不良対策、省スペース化など課題解決と関わります。
射出成形工場の省人化に役立つダウンロード資料
クリックすると該当のコンテンツに内部リンクします
省人化と省力化の違い
省人化
- 目的:設備化により生産性向上や人手不足の課題を解決すること
- 目標:作業に必要な人員を減らす
- 手段:業務を見直し、省ける/自動化できる工程を効率化する
- 方法:自動化の設備を導入する
- 事例:人の作業による成形品包装を自動包装へ
省力化とは
- 目的:設備やITツールなどの導入で業務を効率化すること
- 目標:手間や労力をできるだけ省く
- 手段:業務を見直し、簡素化できる工程を効率化する
- 方法:効率化できる設備やツールを導入する
- 事例:射出成形の工程を総合管理するツールによる管理で効率化
初めての工場省人化の悩み
- どの工程から工場省人化を始めたらいいのか
- どの工程なら省人化できそうか
- どの工程なら省人化の効果が大きいのか
- 工場を省人化したいが、いきなり大きな投資はできない
- 既存の射出成形ラインを活かし、まずは部分的に省人化をしたい
射出成形工程それぞれの省人化が重要
射出成形の工程は多岐にわたり、それぞれの省人化が重要です。
射出成形の工程
- 原料の粒断・混合
- 射出成形
- 取出工程
- 成形品ストック・搬送
- 乾燥工程
- 検査・梱包
- 材料搬送
このページでは「工場の省人化」による改善事例の記事をまとめてご案内します。
射出成形業務の課題解決にお役立てください。
工場省人化に役立つダウンロード資料
原料の粒断・混合の省人化
製造原価を低減する10のチェックリスト
射出成形の製造原価を低減するには、樹脂材料のリサイクル率を向上させることが有効です。この資料では10個のチェックリストをまとめていますので、リサイクル率の向上や製造原価の低減にお役立てください。

取り出し工程の省人化
サイクルタイムを短縮する取り出しロボット
射出成形品の取出し工程は取出しタイムを短縮することで、1ショットのサイクルタイムが大きく変わります。
この資料ではサイクルタイムや段取り時間の短縮、さらに、耐久性やメンテナンス性にも着目しているハーモの取出しロボットをご紹介しています。

チャック板交換の手間やミスを解決するハーモのオリジナル製品
チャック板交換でお悩みを抱える方におすすめのオリジナル製品をご紹介します。

材料搬送の省人化
人手不足を改善する成形品自動ストッカー
射出成形品のストック・箱詰め作業を人手で行うのは、作業者にとって大変な作業です。
この資料では低コストで、限られたスペースにも簡単に設置ができ、人手不足の解消やストック工程の精度向上に貢献する成形品自動ストッカーをご紹介します。

乾燥工程の省人化
成形品不良率を大きく改善する4つの周辺機器
射出成形の周辺機器を工夫することで、成形品の品質改善に繋がることがあります。
この資料では60年以上の工程改善のノウハウをもとに、射出成形の前後工程で品質向上に貢献する周辺機器をご紹介しています。

検査・梱包の省人化
1万個の成形品袋詰めを40秒で可能にする自動包装機
成形品の袋詰め作業は付きっ切りの作業になるため作業コストが大きい工程です。
この資料では袋詰め工程を自動化し、作業コストやホコリ等の混入を防ぎ品質を改善した事例をご紹介します。

成形工程全般の管理・効率化
射出成形の生産ラインを一括管理するハーモの『トータルリンク』
射出成形で無駄を無くしたい、品質を改善したい、コストを抑えたい…そんなお悩みをお持ちのご担当者様。射出成形機の周辺機器の設定・起動・モニタを一括管理できる「トータルリンクシステム」をご存知ですか。
この資料では射出成形工程の一括管理で品質向上とコスト低減を実現する設備『トータルリンク』についてご説明しています。


射出成形工場レイアウト改善
資料内容
- 生産品目を考える
- 工場内の導線を考える
- 面積生産性を考える
- 工程入れ替えの柔軟性を考える
- 外乱による影響を考える
- 安全衛生を考える
- 管理のしやすさを考える

以下の工場省人化の記事をご用意しています
原料の粒断・混合の省人化事例
射出成形の省人化事例
取り出し工程の省人化改善事例
乾燥工程の省人化事例
検査・梱包の省人化事例
材料搬送の省人化事例
成形工程全般の管理・効率化
射出成形工場レイアウト改善
周辺機器の一括設定・一括起動・一括モニタで射出成形の工程を総合管理し、工場の省人化を実現するのがハーモの『トータルリンク』です。
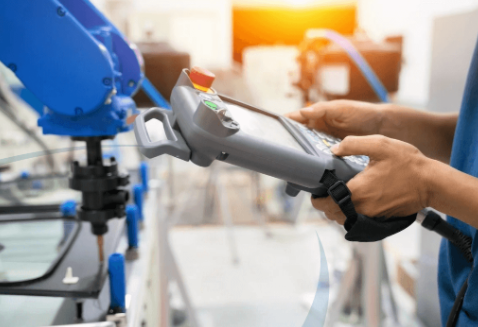
01:射出成形の段取り時間短縮
射出成形の取出しロボットのペンダントで周辺機器を一括で起動・停止・設定
02:射出成形のヒューマンエラー防止
射出成形の取出しロボットが作業開始時刻を自動計算、さらに設備接続の間違いをお知らせ
03:射出成形の不良率低減
射出成形の取出しロボットが材料や周辺機器の異常を監視し、自動で設備を制御
04:射出成形の設備異常トレーサビリティ
射出成形の取出しロボットや周辺機器の異常履歴・稼働データが確認
05:射出成形の製造原価低減
ロボットが終了時刻を自動計算して、材料供給を最小限に制御
トータルリンクについてはこちらをご覧ください。

射出成形品の不良発生コストの改善例
生産設備の設定ミスや停止に気づかなかったことによる機会損失を防止
20,000円 × 6時間 = 年間 約120,000円
射出成形の不良原因究明コストの改善例
納品した成形品でクレームが発生したことによる機会損失を防止
(20,000円 + 12,000円) × 24時間 = 年間 約768,000円
成形材料段取り替えコストの改善例
段取り替え時の余分な材料供給による機会損失を防止
35,000円 × 10台 × 12ヶ月 = 年間 約4,200,000円
トータルリンクの導入で
年間 約5,100,000円の コスト改善が期待できる。